Construction sites are notorious as dangerous places, mainly with workers exposed to risks such as heavy machinery, heights, and unpredictable weather. These hazards can lead to accidents, injuries, and even fatalities, causing delays and raising costs. Since it is a responsibility to improve safety, many are turning to one safe concept known as ‘Prefabricated Construction’, a method that reduces on-site labour and minimises potential dangers. As the demand for safer, more efficient building practices grows, prefabricated construction is emerging as a monumental step forward in the construction industry.
This article will dive into the key benefits of prefabricated construction.
This article will dive into the key benefits of prefabricated construction.
What is Prefabricated Construction?
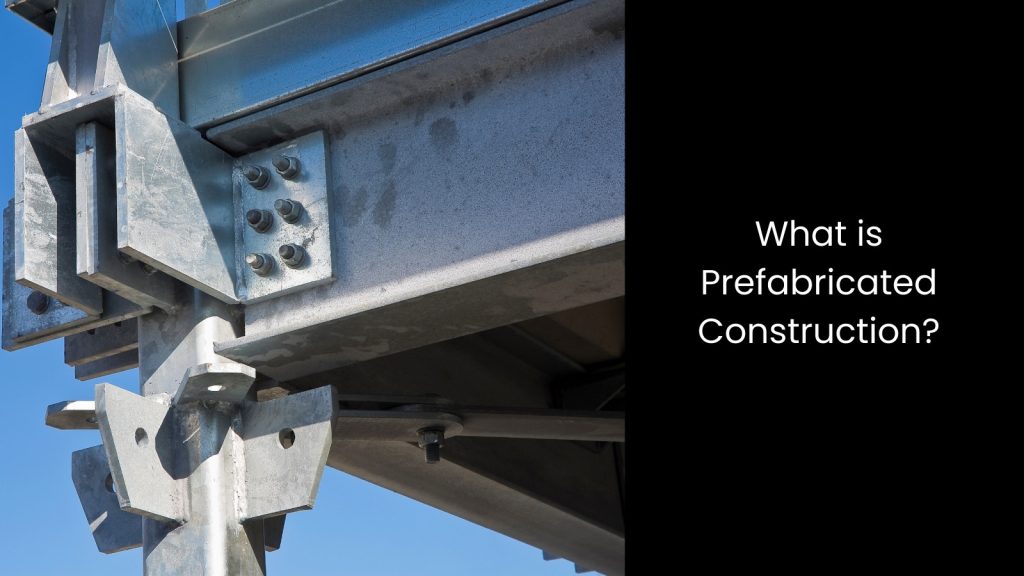
- Prefabricated construction refers to the method of assembling building components off-site in a controlled factory environment before transporting them to the construction site for assembly. This approach is unique because it focuses on manufacturing elements such as walls, floors, and roofs ahead of time, unlike traditional construction, where workers build everything directly on-site.
- This offers several advantages, including faster project completion. Since components are made in a factory setting, work progresses regardless of weather conditions. It also reduces on-site labour and minimises disruptions in the surrounding area. The process is more efficient because it allows for better quality control, as factories can maintain consistent standards.
- You know that those traditional constructions usually face delays and complications from unpredictable site conditions. However, this is not a matter for prefabricated construction, as it remains more predictable and streamlined.
- Additionally, this method is more cost-effective in the long run due to reduced labour costs and material waste. The ability to customise components while ensuring high quality makes prefabricated construction a preferred choice in modern building projects. It is also more environmentally friendly since fewer materials are wasted, and construction waste is minimised compared to the conventional approach. These factors make prefabricated construction an increasingly popular option across various industries, offering a blend of speed, cost savings, and sustainability.
Understanding Key Benefits of Prefabricated Construction
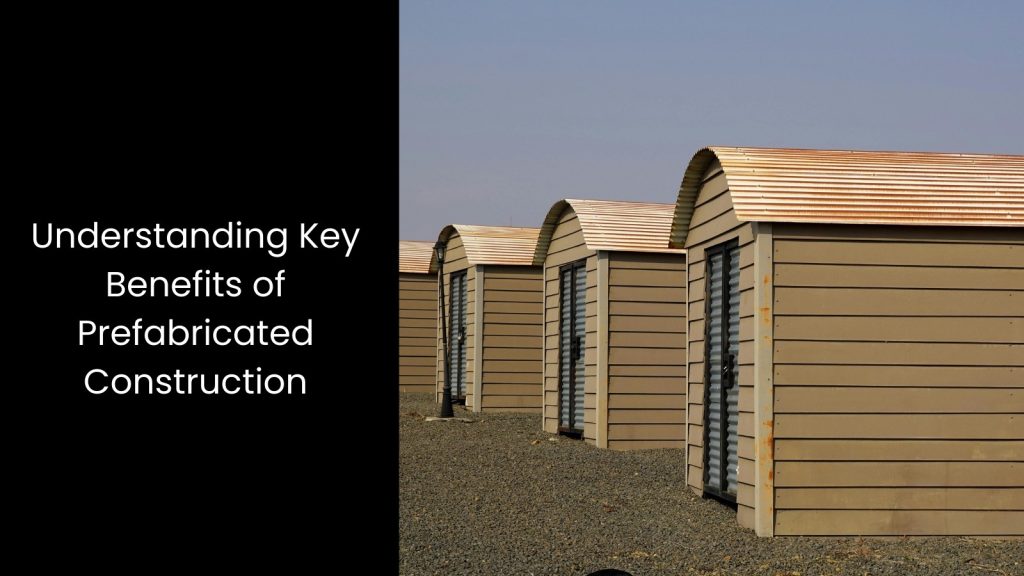
Less Site Disruption
Disruption and construction are just two things that are interwoven. However, prefabricated construction changes that. Since most of the work happens off-site in a factory, the actual on-site construction activities are minimal. This approach significantly reduces noise, dust, and other disturbances that usually come with traditional building methods.
Prefabricated construction eliminates the need for long hours of heavy machinery and manual labour at the site, keeping the surrounding area quieter and cleaner. This way, people living near construction zones can experience fewer interruptions in their daily lives, making the environment more comfortable.
Prefabricated construction also limits the amount of waste and materials left on-site, which helps in keeping the area tidy. While traditional methods normally take months of work on-site, the quick assembly of prefabricated components speeds up the process. This means workers spend less time on-site, causing disruptions. The short timeline also lessens the impact on traffic, local businesses, and residents. This will lead to a smoother, more organised construction experience.
With fewer people and machinery on-site, prefabricated construction helps reduce the environmental footprint of the project. This method not only makes construction more efficient but also ensures the local community is less disturbed throughout the process.
Prefabricated construction eliminates the need for long hours of heavy machinery and manual labour at the site, keeping the surrounding area quieter and cleaner. This way, people living near construction zones can experience fewer interruptions in their daily lives, making the environment more comfortable.
Prefabricated construction also limits the amount of waste and materials left on-site, which helps in keeping the area tidy. While traditional methods normally take months of work on-site, the quick assembly of prefabricated components speeds up the process. This means workers spend less time on-site, causing disruptions. The short timeline also lessens the impact on traffic, local businesses, and residents. This will lead to a smoother, more organised construction experience.
With fewer people and machinery on-site, prefabricated construction helps reduce the environmental footprint of the project. This method not only makes construction more efficient but also ensures the local community is less disturbed throughout the process.
Weather-Resistant
When it comes to typical construction methods, weather can cause significant delays and complications. However, prefabricated construction is different from this typical landscape. Why do we say that?
Many components in prefabricated construction are built in climate-controlled factory settings, which protect them from adverse weather conditions like rain, snow, or extreme heat. Since the pieces are produced indoors, the work continues regardless of what is happening outside, ensuring that schedules are met without interruptions. This weather-resistant nature of prefabricated construction allows for faster and more predictable project timelines.
In contrast, traditional construction is more dependent on the weather, and delays due to rain or cold can stretch out the project duration. Also, since prefabricated construction takes place in controlled environments, it reduces the risk of materials being damaged by harsh conditions, like wood warping or concrete curing incorrectly.
The ability to work without concern for unpredictable weather makes prefabricated construction not only more reliable but also cost-effective, as it avoids the extra costs tied to weather-related delays. This weather-resistant advantage takes centre stage in making prefabricated construction an efficient choice for projects, especially in regions with extreme or variable weather patterns.
Many components in prefabricated construction are built in climate-controlled factory settings, which protect them from adverse weather conditions like rain, snow, or extreme heat. Since the pieces are produced indoors, the work continues regardless of what is happening outside, ensuring that schedules are met without interruptions. This weather-resistant nature of prefabricated construction allows for faster and more predictable project timelines.
In contrast, traditional construction is more dependent on the weather, and delays due to rain or cold can stretch out the project duration. Also, since prefabricated construction takes place in controlled environments, it reduces the risk of materials being damaged by harsh conditions, like wood warping or concrete curing incorrectly.
The ability to work without concern for unpredictable weather makes prefabricated construction not only more reliable but also cost-effective, as it avoids the extra costs tied to weather-related delays. This weather-resistant advantage takes centre stage in making prefabricated construction an efficient choice for projects, especially in regions with extreme or variable weather patterns.
Reducing Environmental Impact
It is not a secret that the global construction industry tries harder to minimise its impact on the environment. This is where we entered the realm of prefabricated construction, which plays a big role in this effort.
With prefabricated construction, the process is much more efficient. Shorter construction timelines mean that the project uses fewer resources, which leads to less energy consumption. The time saved also reduces the amount of machinery running on-site, which directly decreases pollution and fuel usage.
Apart from that, prefabricated construction produces less material waste. Since the components are made in factories, they can be produced with precision. This will ensure that only the necessary materials are used. The factory setting also allows for better recycling and reusing of materials, which traditional construction methods do not always manage as efficiently. This approach keeps waste to a minimum, helping to reduce the overall environmental footprint of the project.
Since prefabricated construction happens off-site, there is also less disruption to the land around the construction area, preserving natural habitats. These combined efforts result in a more sustainable construction process, which benefits both the environment and the community. As environmental concerns grow, prefabricated construction provides an innovative and eco-friendly solution to the world.
With prefabricated construction, the process is much more efficient. Shorter construction timelines mean that the project uses fewer resources, which leads to less energy consumption. The time saved also reduces the amount of machinery running on-site, which directly decreases pollution and fuel usage.
Apart from that, prefabricated construction produces less material waste. Since the components are made in factories, they can be produced with precision. This will ensure that only the necessary materials are used. The factory setting also allows for better recycling and reusing of materials, which traditional construction methods do not always manage as efficiently. This approach keeps waste to a minimum, helping to reduce the overall environmental footprint of the project.
Since prefabricated construction happens off-site, there is also less disruption to the land around the construction area, preserving natural habitats. These combined efforts result in a more sustainable construction process, which benefits both the environment and the community. As environmental concerns grow, prefabricated construction provides an innovative and eco-friendly solution to the world.
Faster Construction Time
Prefabricated construction stands out for its ability to speed up building projects.
Since the industry tends to manufacture prefabricated components off-site in factories, much of the work occurs before the construction team even reaches the site. These components, such as walls, floors, and roofs, are built in a controlled environment where there are fewer delays.
Once they are ready, they are quickly transported to the site and assembled, drastically cutting down the time needed to complete the building. This process reduces the amount of on-site labour, which is usually slowed down by weather, site conditions, or other external factors in traditional construction.
As a result, prefabricated construction leads to faster project timelines, and it will allow buildings to be completed in a fraction of the time. The quick assembly of prefabricated components also reduces downtime and ensures that the project stays on track. Not to mention that this benefits both developers and clients who want faster results.
Since the industry tends to manufacture prefabricated components off-site in factories, much of the work occurs before the construction team even reaches the site. These components, such as walls, floors, and roofs, are built in a controlled environment where there are fewer delays.
Once they are ready, they are quickly transported to the site and assembled, drastically cutting down the time needed to complete the building. This process reduces the amount of on-site labour, which is usually slowed down by weather, site conditions, or other external factors in traditional construction.
As a result, prefabricated construction leads to faster project timelines, and it will allow buildings to be completed in a fraction of the time. The quick assembly of prefabricated components also reduces downtime and ensures that the project stays on track. Not to mention that this benefits both developers and clients who want faster results.
Cost-Effective
The latter is a cost-effective option for many building projects. The reason is that this method helps reduce labour costs because much of the work happens off-site in a factory, where production is more efficient and requires fewer workers.
On top of that, prefabricated construction uses fewer materials, which cuts down on waste. The components are designed and built to fit together perfectly, which eliminates excess materials and minimises mistakes that lead to unnecessary spending.
Shorter construction periods also save money. With prefabricated construction, projects move quickly from start to finish, reducing the time workers spend on-site and cutting labour expenses. Since assembly is faster and requires less on-site effort, it helps avoid delays and costly overtime.
These factors combined make prefabricated construction a more affordable choice than traditional construction methods. This capacity makes it an attractive solution for developers looking to stay within budget while still maintaining quality.
On top of that, prefabricated construction uses fewer materials, which cuts down on waste. The components are designed and built to fit together perfectly, which eliminates excess materials and minimises mistakes that lead to unnecessary spending.
Shorter construction periods also save money. With prefabricated construction, projects move quickly from start to finish, reducing the time workers spend on-site and cutting labour expenses. Since assembly is faster and requires less on-site effort, it helps avoid delays and costly overtime.
These factors combined make prefabricated construction a more affordable choice than traditional construction methods. This capacity makes it an attractive solution for developers looking to stay within budget while still maintaining quality.
Optimising Prefabricated Construction Projects Using AI Technology
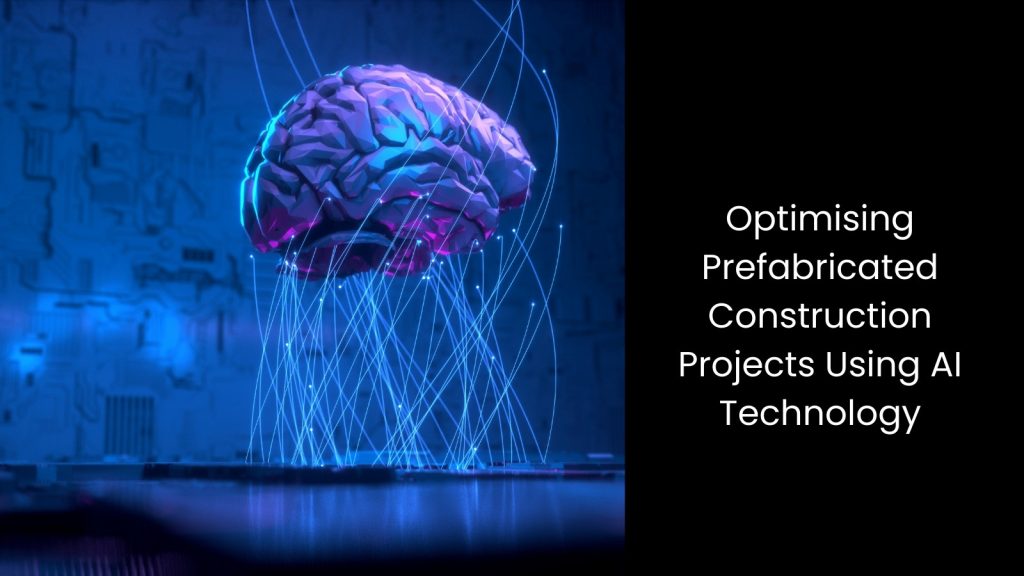
As a result of AI dominance, it now offers transformative opportunities to optimise prefabricated construction projects. From predictive analytics to real-time adjustments, AI ensures that these projects are completed faster, with fewer errors, and at lower costs. Embracing AI-driven software solutions purchased from industry pioneers is a smart choice for construction leaders who want to stay competitive and deliver high-quality projects efficiently.