Also known as Industrial air compressors, mechanical air compressors are essential for generating pressure in compressible fluids or gasses, although in this case, it is air. They are versatile equipment used in a range of industries for multiple purposes. Its primary focus is reducing the air volume to increase the pressure. Common air compressor tools include paint sprayers, abrasive blast equipment, air conditioning and refrigeration. The pressurised air provided by compressing is more potent than atmospheric pressure. This makes it easy to complete certain essential tasks required in an industry. This blog will explain some of Australia’s most popular air compressors.
Why Are Air Compressors Important?
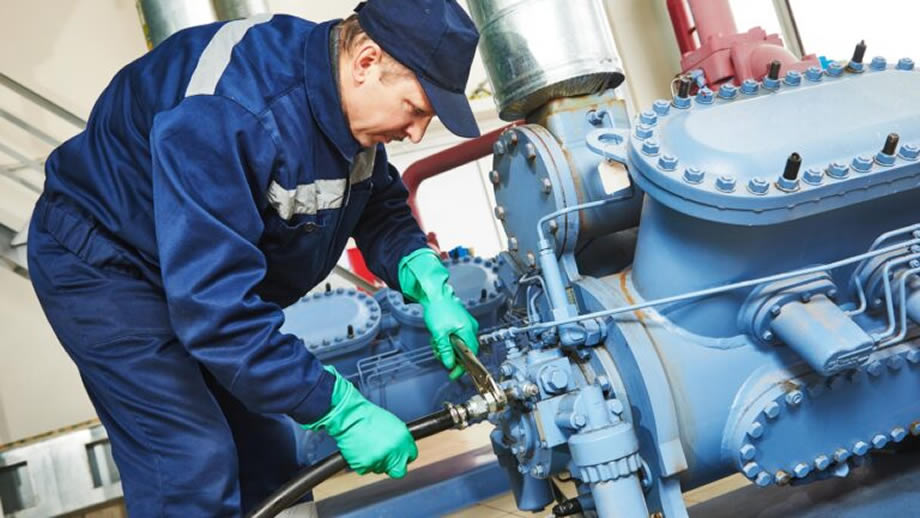
Air compressors are essential mechanical tools in factories and workshops. It forces atmospheric air using pressure to create energy that can be used for later. This energy is converted into usable kinetic energy and can be infused to power multiple pneumatic tools. The process of air compressors requires air to be drawn, which creates a vacuum to reduce its volume. This vacuum afterwards pushes the air out of the chamber, transferring it into its storage tank. When this storage tank reaches maximum air pressure. Once this energy is used, the compressor will be turned back on. The science behind this is that as air is a gas mixture that primarily contains nitrogen and oxygen, it consists of different air molecules with a specific amount of kinetic energy. Hence, when air is compressed, the temperature increases and traps it in a space to bring the molecules closer to each other. The closeness of such molecules is what releases energy.
Compressed air is used as energy (energy air) and as part of a process. (active air). While the former focuses on storing and transmitting energy to do mechanical work, the latter is an important aspect of a certain process.
Three Essential Mechanical Air Compressors
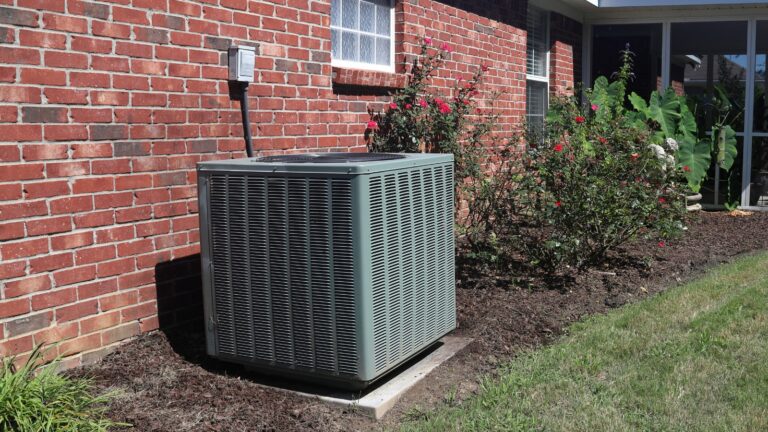
Air compressors come in various shapes and sizes and can be found almost anywhere, including in a person’s garage. Compressors are typically classified as low-pressure, medium-pressure, and high-pressure air compressors. They each have a discharge pressure of 150 psi or less, 151 to 1000 psi and above 1000 psi, respectively. Here are three of the most popular air compressors used in Australia.
Oil Lubricated Air Compressors
Oil Lubricated compressors are a common type of air compressors industrial applications rely on. It is used in various industries, including manufacturing, waste management, recycling and more. Air compressors of this type are cost-effective, long-lasting compressed air solutions suitable for light to heavy-duty industrial applications. As noted by the name, they require oil to keep the production process running smoothly. The lubricated compressor itself can have different types, such as screws, lobes, vanes, liquid rings and more. These forms of compressors, however, require more maintenance for them to work optimally. They are also comparatively heavier. It is nevertheless regarded to be much better than oil-free air compressors, which tend to become warm as there is no oil to cool the components leading to a lower durability period. Moreover, oil-lubricated air compressors produce less noise, which is one main reasons consumers opt for these types of air compressors.
Rotary Screw Air Compressor
A widely used air compressor in industrial work, rotary screw air compressors use rotary movements to compress the air. Using a male and female rotor, which are unique to one another, the compressor traps air within when it is turned on in unison. The trapped air in the cavities between the rotors moves the air down a camber which decreases in size and is moved away from the opening valve. The more volume that is decreased, the higher the pressure is. Hence, as the pressure within the compressor collects, the air is condensed, triggering the compressor discharge valve to open. It, after that, allows the pressurised air to enter a receiver or a holding tank. This form of air compressor is easy to maintain, guarantees continuous air flow and pressurisation, can operate in challenging conditions, is energy efficient and emits low noise.
Piston Air Compressor
Also known as reciprocating compressors, these compressors rely on the reciprocating action of one or more pistons to compress air within a cylinder and discharge it. It is a positive-displacement air compressor that decreases air volume while increasing density. Here, gas first enters the cylinder through an intake valve, after which the pistons move aside to let the gas pass into the cylinders. A crankshaft is secondly used to power the piston to compress the gas in one stroke of pressure. The compressed air is lastly sent into a storage tank for use. Two-stage unit piston air compressors can be used if the company requires higher air pressures. The only difference in the latter is that compressed air enters the second stage and passes through an intercooler to remove heat generated during the first stage. This is a cost-effective air compressor that requires low maintenance.
Maintenance of Air Compresses is Key to Reap its Benefits
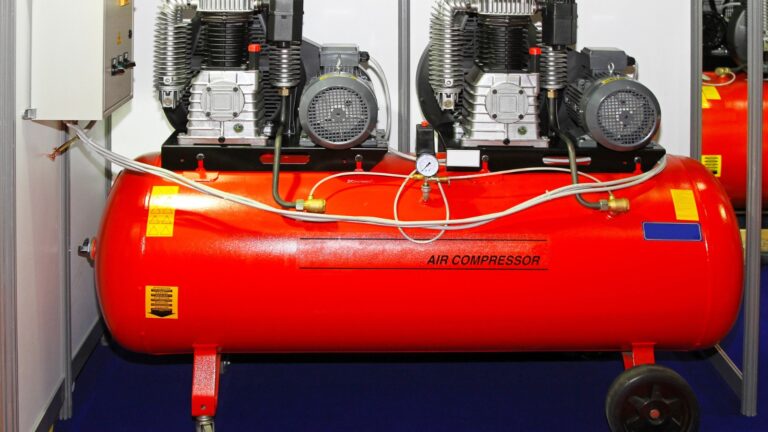
Whichever air compressor you invest in, it is important to track its health and provide the necessary maintenance it needs at the right time. In an industrial environment, this may be hard to do with the number of assets in a company. Hence, investing in a robust asset management solution is integral to guarantee that your mechanical assets are functioning well. Failing to do so will not only mean that your compressors will not be doing what it is meant to do properly but could, at times, create a dangerous work environment.