In this article, we will reveal the consequences of poor mechanical asset management and the practical solutions to keep your machines of top quality.
What Does it Refer to as 'Mechanical Asset Management'?
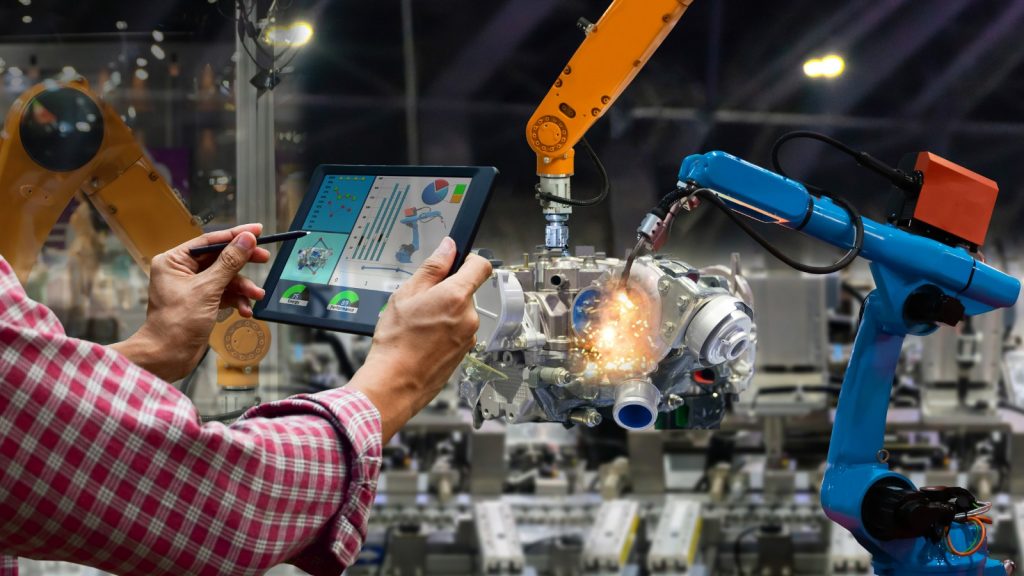
- You may have heard of this thousands of times, especially if you belong to the construction or industrial sector. However, we thought of bringing a rough idea for your convenience. Mechanical asset management means the systematic oversight, maintenance, and optimisation of physical machinery and equipment within an organisation. It includes a comprehensive way of managing resources to ensure their dependability, durability, and operational effectiveness over every phase of their lifespans.
- But have you ever thought why is this management so complicated? That is because this practice spreads over a broad range of responsibilities from strategic planning, maintenance schedules, and utilising technology like IoT sensors to data analytics to monitor asset health in real time.
- Let us explain what you would receive through proper mechanical asset management. When you are on the right path to effective mechanical asset management, it aims to minimise downtime by implementing preventive maintenance measures. It also helps identify potential issues before they escalate into failures and then optimises the performance of machinery.
- That is not all! It also involves tracking asset usage and conducting regular inspections on the assets you employ within your business premises. This strategic approach can be known as a preventive landscape as it will help you to enhance productivity, reduce costs, and maximise the value of mechanical assets within a business or industrial setting.
- Now let us explain the darker side of poor mechanical asset handling. There will be more breakdowns, lower operating efficiency, and longer downtime as a result of poor machinery maintenance at the end. On the other hand, it causes unforeseen breakdowns, jeopardised security, and expensive repair bills. As you can see, the performance of machinery weakens due to neglected maintenance schedules and poor care, which affects the overall production and profitability of your business.
Top 5 Practical Solutions for Poor Mechanical Asset Management
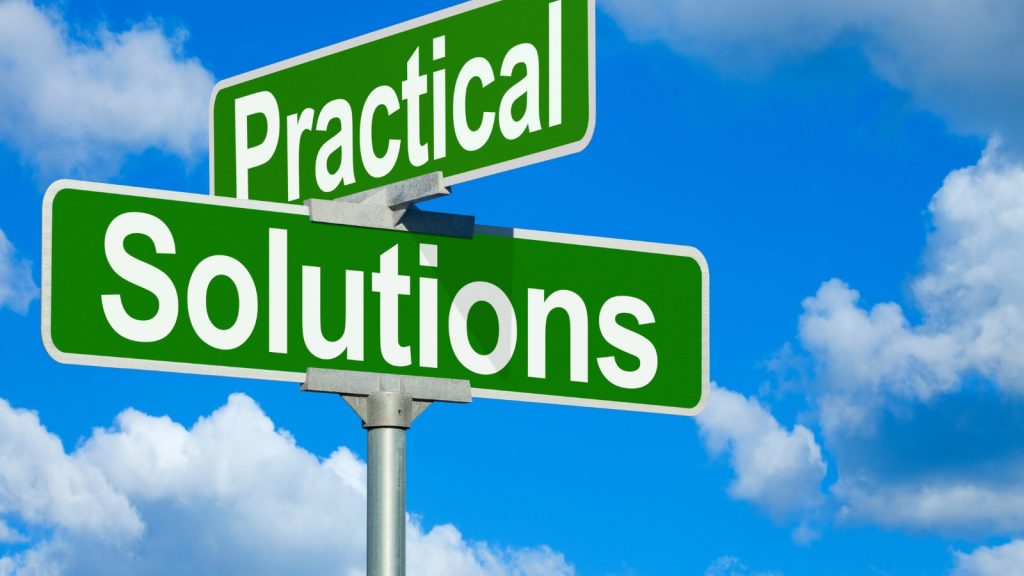
Implementing Failure Analysis
This analysis helps in creating informed maintenance protocols, adjusting schedules, and introducing necessary upgrades to prevent recurring issues. It enables proactive measures, such as replacing faulty components or adjusting operational parameters, mitigating potential failures before they escalate.
Integrating failure analysis into asset management practices not only reduces downtime and repair costs but also fosters a culture of continuous improvement. It allows for data-driven decision-making, enhancing overall asset reliability, extending their lifespan, and optimising operational efficiency within the organisation.
Establishing Performance Metrics
This provides quantifiable benchmarks to gauge asset health and efficiency. By defining Key Performance Indicators (KPIs) such as uptime, mean time between failures, or maintenance costs, organisations gain insights into asset performance.
These metrics aid in evaluating the effectiveness of maintenance strategies, pinpointing underperforming assets, and directing resources towards critical areas. They enable data-driven decision-making, facilitating the identification of problematic machinery, optimising maintenance schedules, and aligning efforts to enhance overall operational effectiveness.
Through continuous monitoring and analysis of these metrics, organisations can adapt maintenance practices, predict potential failures, and significantly improve the reliability and longevity of mechanical assets while reducing unexpected downtimes and associated costs.
Upgrading to Smart Technologies
These advancements facilitate predictive maintenance, identifying potential issues before they escalate, thus minimising downtime and unexpected failures. Moreover, smart technologies offer remote monitoring, allowing for proactive interventions, optimising maintenance schedules, and ensuring timely repairs.
By integrating these innovations, organisations enhance operational efficiency, extend the lifespan of machinery, and streamline asset management processes. This proactive approach not only reduces costs associated with reactive maintenance but also transforms the management of mechanical assets into a more agile and responsive system.
Utilising Predictive Maintenance Techniques
Predictive maintenance transforms asset management from reactive to proactive, enhancing operational efficiency, extending machinery lifespan, and reducing overall maintenance costs.
Through the power of predictive analytics, organisations can prioritise maintenance efforts, maximise asset availability, and ensure the reliability of their mechanical assets, significantly improving their productivity and performance.
Regular Inspections and Audits
This proactive approach minimises unexpected breakdowns, enhances safety, and optimises asset performance. Moreover, audits ensure compliance with maintenance protocols, improving overall asset reliability and extending their operational lifespan.
Through diligent and systematic inspections, organisations foster a culture of preventive maintenance, reducing downtime, optimising resources, and ultimately improving the efficiency and longevity of their mechanical assets.
No More Failures for a Smarter Tomorrow
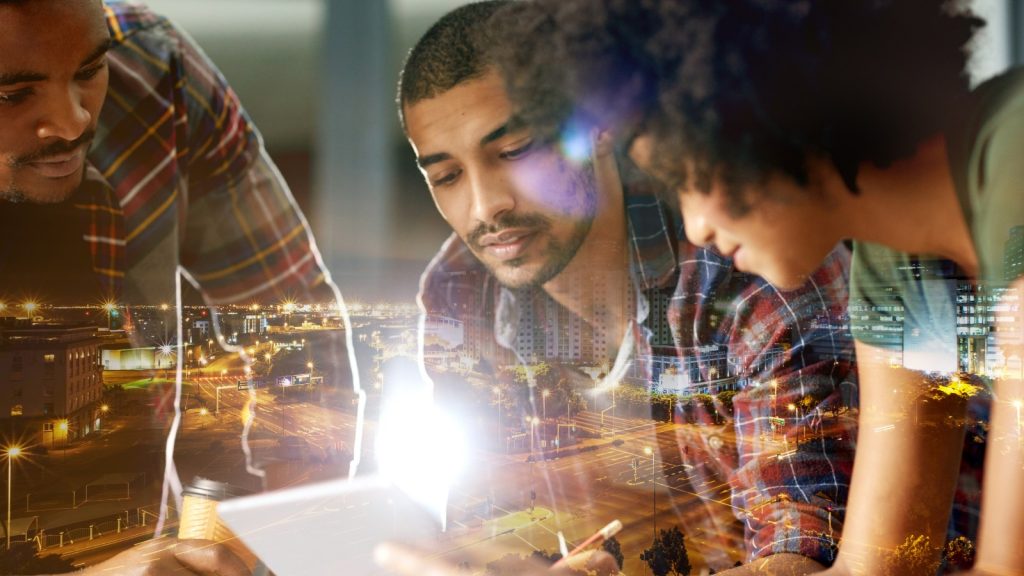
Controlling the quality of the final product or service means you have to take full control of each component of the production procedure. Machinery or mechanical assets are like the heart of your business as you cannot go without their function. Technology is the easiest way to fulfil this requirement within a short time while saving your money as well. If you are still hesitating to hold hands with suitable software solutions, take a moment and think of the benefits it offers you to manage mechanical assets. If you choose an industry expert for this technological collaboration, the benefits will be doubled for sure.