This article discovers those different levels of data integration, highlighting how advanced technologies like Digital Twin are revolutionising how industries manage and utilise data.
What is a Virtual Model?
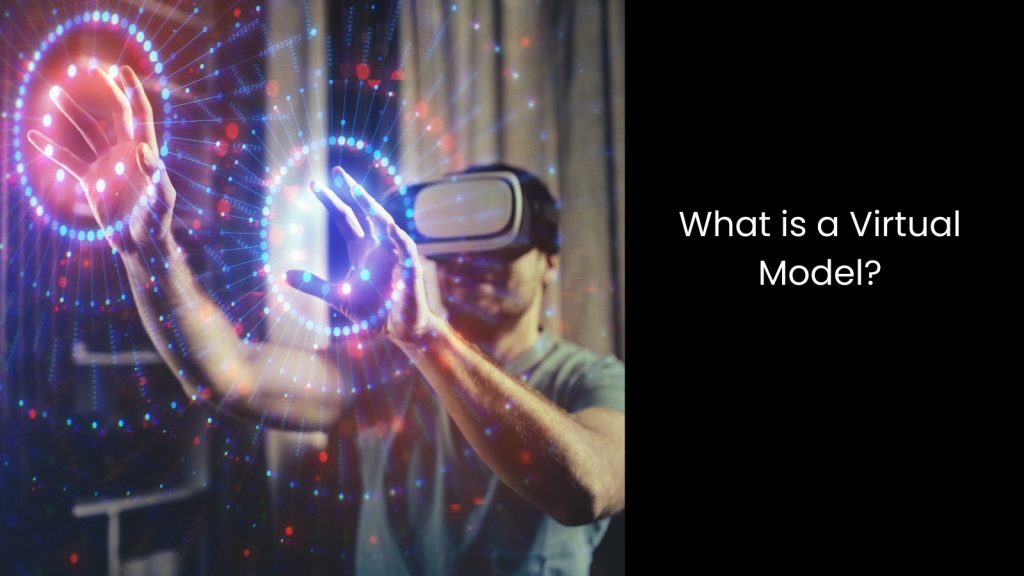
- In fact, this involves creating a detailed digital model of a component, part, or assembly on a computer. This virtual model is a digital representation that mirrors the physical object, allowing engineers and designers to simulate the fabrication process and predict how the part will behave structurally.
- No matter what industry we are talking about, this technology will allow operators to test and refine their ideas in a digital environment before moving on to physical prototyping, reducing the time and cost associated with traditional manufacturing processes. Virtual Model technology supports a wide range of simulations, including stress testing, material behaviour analysis, and even the full manufacturing process. This ensures that the final product meets all design specifications and performance requirements.
- Various technologies can present Virtual Model capabilities, including Digital Twin, which creates digital representations of products, processes, etc., and Computer-Aided Design (CAD) software, which allows users to create and manipulate 3D models of objects. Also, Finite Element Analysis (FEA) software plays a crucial role in analysing the structural integrity of these models under different conditions. Apart from the above, Virtual Reality (VR) and Augmented Reality (AR) technologies can bring these digital models to life by allowing users to interact with them in a more immersive environment.
What is Data Integration?
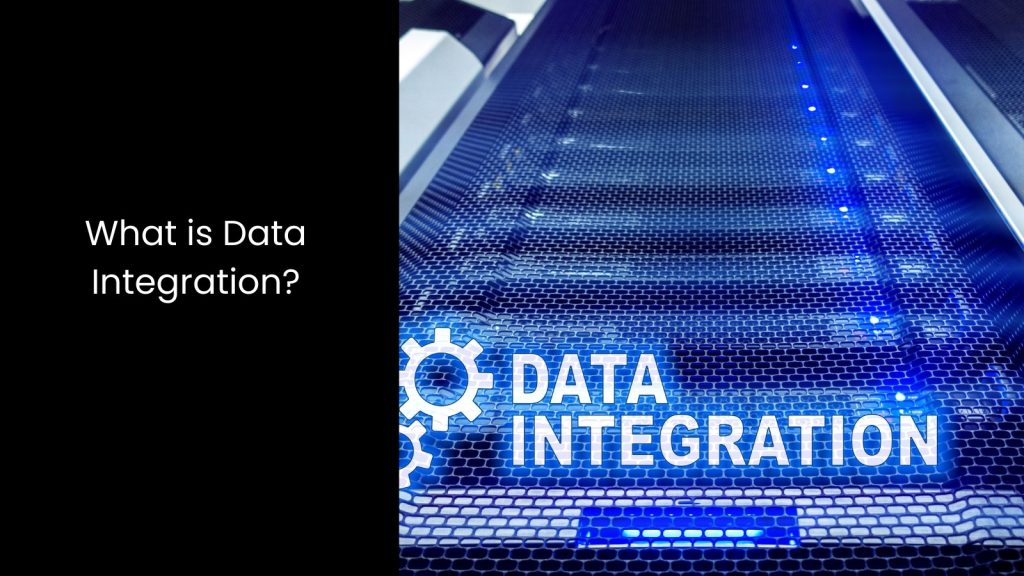
- Data integration in a system revolves around combining data from different sources into a single, unified view. This process allows various data points from multiple databases, applications, or files to work together seamlessly. This will create a comprehensive dataset that organisations can use for analysis, reporting, and decision-making.
- However, why is it so important? When integrating data, businesses ensure that all information across the system aligns and remains consistent, and this enhances the accuracy of insights derived from the data.
- Yet, this is not a simple process. Data integration usually involves several steps, including extracting data from the original sources, transforming it into a consistent format, and then loading it into a central repository where users can access and analyse it. This process, often referred to as ETL (Extract, Transform, Load), is essential for maintaining data quality and making sure that users can trust the information they use.
- Technologies that support data integration include ETL tools, data warehouses, and data lakes. These technologies encourage the merging of structured and unstructured data, making it easier for organisations to gain a complete view of their operations. This means deal-time data integration tools allow businesses to access the most current data.
Levels of Data Integration in a Virtual Model
In the below section, we specifically focus on the Digital Twin’s data integration levels. The latter describes the varying extents of data exchange between a physical component and its digital counterpart. Depending on the integration depth, Digital Twin can be categorised into three distinct subcategories, each reflecting a different level of interaction.
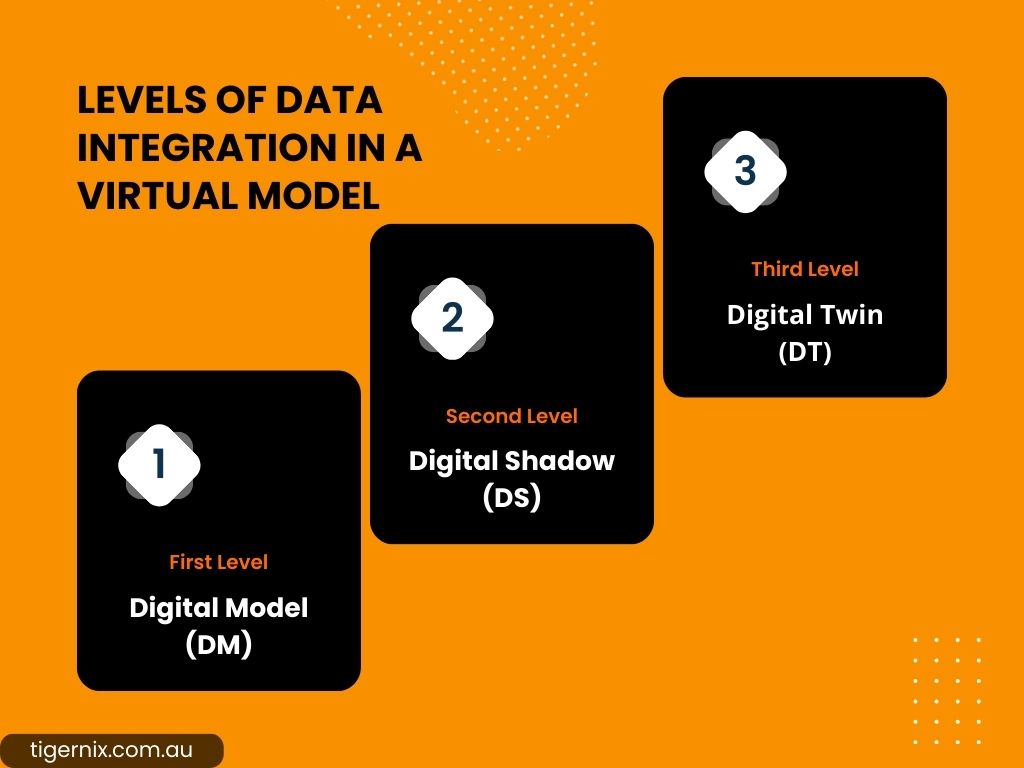
Digital Model (DM)
In this context, the digital model does not have any automated data flow between the physical object and its digital counterpart. This means that if something changes in the physical object, it does not automatically update in the digital model, and vice versa.
Then what does it do? All data transfers between the physical and digital models happen manually, requiring human intervention to ensure that both versions stay in sync. For example, in the construction sector, a digital model could represent anything from a single building component to an entire building.
However, any updates made to the physical building, such as modifications or repairs, do not reflect in the digital model unless someone manually inputs those changes. Similarly, if someone makes adjustments to the digital model, these changes do not impact the physical structure unless someone manually implements them. Because of this lack of automation, the digital model serves more as a static representation than a dynamic, real-time reflection of the physical object.
Not to highlight that this limits its usefulness in scenarios where real-time data and updates are crucial for decision-making. However, it still provides value by offering a visual or digital reference of the physical object, which can be useful for planning, analysis, or documentation purposes.
Digital Shadow (DS)
In a digital shadow, there is an automated data flow from the physical object to its digital counterpart. This means that any changes in the physical object automatically update the digital shadow. However, this connection only works one way.
The Digital Shadow reflects changes in the physical object, but any modifications made to the Digital Shadow do not impact the physical object. For example, if authorities make updates to the physical structure, like adding a new element or modifying a wall, it automatically shows up in the digital representation without needing manual input.
As you can see, this level of integration makes the digital shadow more dynamic and responsive compared to the basic digital model. It allows users to monitor the physical object in real time, providing up-to-date information that can be crucial for maintenance, planning, and analysis.
However, the limitation of a digital shadow is that it remains a one-way street, as we mentioned above. Although it can accurately reflect the current state of the physical object, it cannot influence or control the physical object itself.
Digital Twin (DT)
This two-way data flow creates a dynamic relationship where digital and physical objects constantly interact. It allows real-time monitoring, control, and optimisation beyond any doubt. If we put this more simply, unlike a digital shadow, which only reflects changes from the physical object, a digital twin can influence and control the physical object, making it a powerful tool for predicting and improving performance.
The Digital Twin’s data comes from both the physical environment and virtual models. They are enriched with processes like statistics and regression analysis, making them more data-rich than a digital shadow. This abundance of data is what makes the Digital Twin provide deeper insights and more accurate predictions, supporting better decision-making.
Creating Space for Smooth Data Integration via the Best Virtual Model Technologies
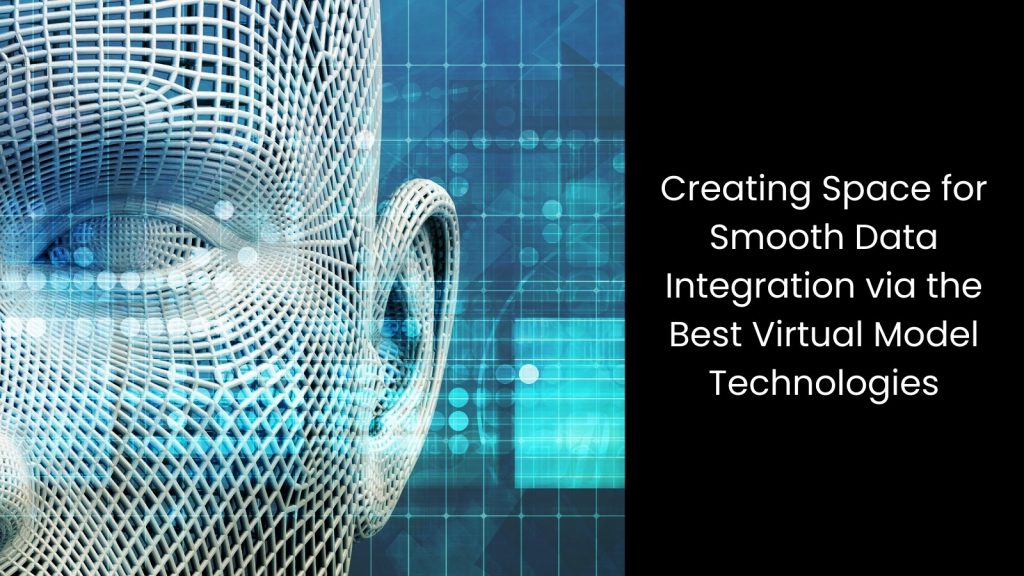
Since you have read this article, you know that effective data integration requires choosing the right virtual model technologies. If you opt for advanced tools like Digital Twin, you can ensure a seamless data flow between physical and digital assets, enhancing accuracy and decision-making. It is not a boast if we say Digital Twin stands out as a top choice in the industrial world in Australia.