With technology advancing, a mega industrial setting running at peak efficiency is no longer a mere dream in 2025. We have entered a digital realm where every valve, pump, and pipe sends live updates to a central system, and the operations occur without delays. This is possible now due to the impact of wireless sensor networks (WSNs) in industrial automation. Globally, industries adopting WSNs have seen operational efficiency rise, transforming how processes are managed. Unlike traditional wired systems, WSNs monitor equipment and processes in real-time, going beyond traditional limitations.
This article explores how wireless sensor networks revolutionise industrial automation, making efficiency goals a reality.
This article explores how wireless sensor networks revolutionise industrial automation, making efficiency goals a reality.
We will look into
- What are Wireless Sensor Networks?
- Key Ways Wireless Sensor Networks Enhance Efficiency in Industrial Automation
- Process Automation
- Data Analytics Enhancement
- Flexibility in Deployment
- Interoperability
- Real-Time Monitoring and Pinpointing Areas of Errors
3. Utilising Advanced Wireless Sensor Networks for Optimised Industrial Efficiency
What are Wireless Sensor Networks?
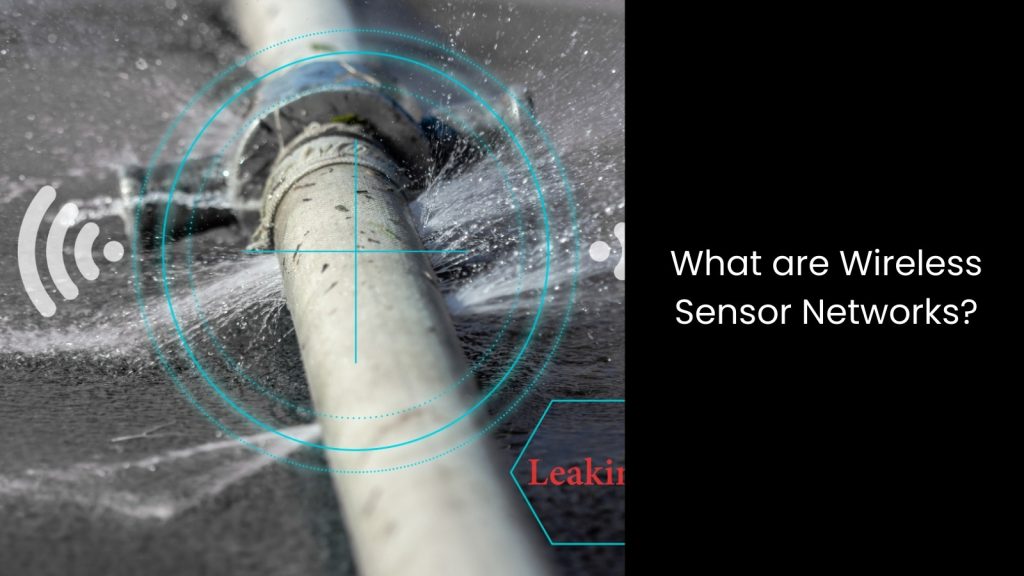
- Wireless sensor networks, or WSNs, are interconnected sensors that collect and transmit data wirelessly to a central system or dashboard.
- So, what is the difference between old sensor networks and wireless sensors? Unlike wired sensors, which rely on physical cables for data transmission, WSNs use wireless communication, offering flexibility in deployment and cost savings by eliminating extensive wiring. These networks play a key role in the Internet of Things (IoT), where sensors gather real-time data and send it to central dashboards for monitoring and analysis.
- The IoT enhances this process as it enables instant connectivity and data sharing, allowing industries to track operations and make informed decisions faster.
- WSNs have become widely used in large-scale industries due to their ability to monitor complex systems, optimise energy consumption, and improve safety. Industries value the convenience of remote monitoring, and the efficiency gained through real-time insights.
- With its full potential, these wireless sensor networks empower industries with scalable, adaptable solutions that streamline automation and support smarter, faster, and more reliable industrial processes.
Key Ways Wireless Sensor Networks Enhance Efficiency in Industrial Automation
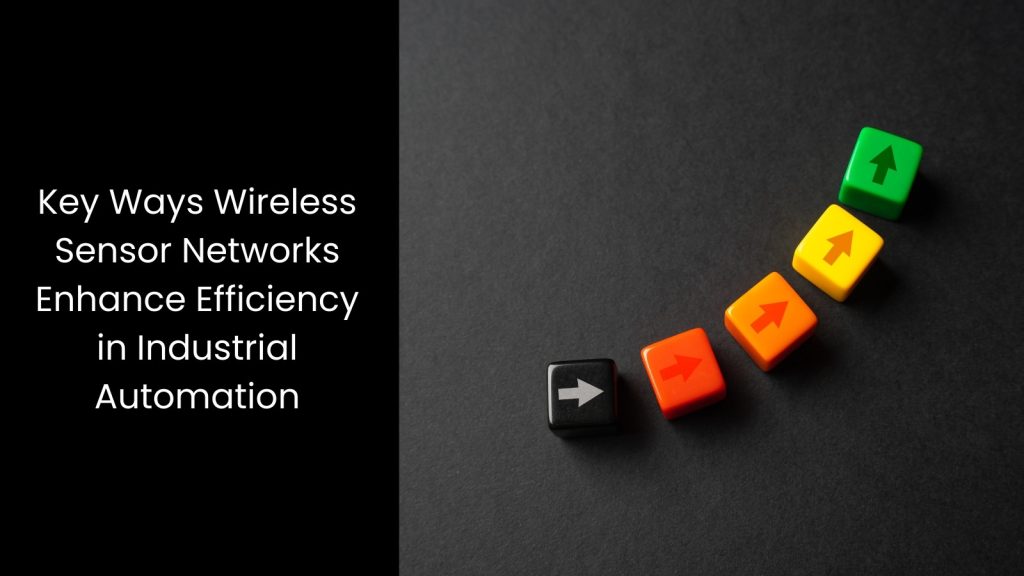
Process Automation
This stands out as one of the most important ways WSNs enhance efficiency in industrial automation, especially in large-scale operations like water treatment plants, electric powerhouses, and wastewater facilities.
Let us explore how this works.
Wireless sensor networks gather accurate and timely data from sensors across various systems, enabling industrial systems to make automated decisions and perform precise controls. These sensors monitor factors such as pressure, temperature, flow rates, and chemical levels, transmitting the data in real-time to centralised dashboards. This constant stream of information helps industries automate routine tasks like adjusting pump speeds, balancing energy loads, and regulating chemical dosages.
For example, in a water treatment plant, WSNs streamline processes by ensuring filtration systems adjust to changing water quality without human intervention. Likewise, electric powerhouses rely on WSNs to efficiently balance energy loads across grids, reducing waste and preventing overloads.
This way, wireless sensor networks transform industrial automation by connecting processes, empowering industries to maintain efficiency, and ensuring reliable operations in large and complex settings.
Let us explore how this works.
Wireless sensor networks gather accurate and timely data from sensors across various systems, enabling industrial systems to make automated decisions and perform precise controls. These sensors monitor factors such as pressure, temperature, flow rates, and chemical levels, transmitting the data in real-time to centralised dashboards. This constant stream of information helps industries automate routine tasks like adjusting pump speeds, balancing energy loads, and regulating chemical dosages.
For example, in a water treatment plant, WSNs streamline processes by ensuring filtration systems adjust to changing water quality without human intervention. Likewise, electric powerhouses rely on WSNs to efficiently balance energy loads across grids, reducing waste and preventing overloads.
This way, wireless sensor networks transform industrial automation by connecting processes, empowering industries to maintain efficiency, and ensuring reliable operations in large and complex settings.
Data Analytics Enhancement
This occurs especially in mega settings like manufacturing plants, power grids, and water treatment facilities.
Wireless sensor networks continuously collect and transmit large volumes of real-time data from machinery, pipelines, and production systems. These networks provide a wealth of data for advanced analytics to improve process optimisation and efficiency.
Inside industrial plants, WSNs track equipment performance, energy usage, and production output, allowing analytics systems to detect inefficiencies and recommend adjustments instantly. Power grids use WSNs to monitor load distribution and predict potential failures, ensuring smooth and balanced operations.
If we consider water treatment facilities, sensors measure parameters like turbidity, flow rates, and chemical levels, enabling analytics platforms to optimise purification processes while reducing energy consumption. With WSNs, industries gain deeper insights into operational patterns, uncover trends, and make smarter decisions that enhance productivity and resource allocation.
It is indeed a strategic way to connect the dots between data and action, making them essential for modern, efficient industrial automation.
Wireless sensor networks continuously collect and transmit large volumes of real-time data from machinery, pipelines, and production systems. These networks provide a wealth of data for advanced analytics to improve process optimisation and efficiency.
Inside industrial plants, WSNs track equipment performance, energy usage, and production output, allowing analytics systems to detect inefficiencies and recommend adjustments instantly. Power grids use WSNs to monitor load distribution and predict potential failures, ensuring smooth and balanced operations.
If we consider water treatment facilities, sensors measure parameters like turbidity, flow rates, and chemical levels, enabling analytics platforms to optimise purification processes while reducing energy consumption. With WSNs, industries gain deeper insights into operational patterns, uncover trends, and make smarter decisions that enhance productivity and resource allocation.
It is indeed a strategic way to connect the dots between data and action, making them essential for modern, efficient industrial automation.
Flexibility in Deployment
Gone are the days when industrial folks had to struggle with bulky cables and wiring to set up sensors in tough locations. WSNs bring unmatched flexibility in deployment, making them a revolutionising movement for industrial automation.
You know that traditional wired sensor networks made it nearly impossible to monitor hard-to-reach or hazardous areas like high ceilings, deep pipelines, or remote sections of manufacturing plants. WSNs eliminate this issue by enabling sensors to be installed in such challenging spots without needing physical connections. This improvement enhances overall coverage and ensures every corner of an industrial facility gets monitored.
For example, in oil refineries, wireless sensor networks monitor pressure levels in remote pipelines, reducing the risk of undetected leaks. Power plants use WSNs to track heat and vibration in dangerous zones, ensuring safe and efficient operations. Water treatment facilities rely on wireless networks to monitor water quality in isolated tanks or basins without the hassle of extensive wiring. This flexibility speeds up installation, cuts costs, and allows industries to scale their monitoring systems easily.
It is evident that wireless sensor networks transform industrial automation by creating systems that adapt to the most challenging environments, improving efficiency, and ensuring operations stay safe and reliable.
You know that traditional wired sensor networks made it nearly impossible to monitor hard-to-reach or hazardous areas like high ceilings, deep pipelines, or remote sections of manufacturing plants. WSNs eliminate this issue by enabling sensors to be installed in such challenging spots without needing physical connections. This improvement enhances overall coverage and ensures every corner of an industrial facility gets monitored.
For example, in oil refineries, wireless sensor networks monitor pressure levels in remote pipelines, reducing the risk of undetected leaks. Power plants use WSNs to track heat and vibration in dangerous zones, ensuring safe and efficient operations. Water treatment facilities rely on wireless networks to monitor water quality in isolated tanks or basins without the hassle of extensive wiring. This flexibility speeds up installation, cuts costs, and allows industries to scale their monitoring systems easily.
It is evident that wireless sensor networks transform industrial automation by creating systems that adapt to the most challenging environments, improving efficiency, and ensuring operations stay safe and reliable.
Interoperability
Sensors are the devices that bring the hidden messages of industrial systems to life, and wireless sensor networks make this process smarter with their ability to integrate seamlessly with other IoT devices and systems, creating a cohesive industrial automation ecosystem.
Traditional wired sensor networks usually cause headaches due to their lack of compatibility with newer technologies and rigid setups. Industries struggled to connect sensors to advanced systems or add new devices without major rewiring, slowing progress and increasing costs. Wireless sensor networks eliminate these issues by offering smooth interoperability, allowing industries to link sensors with IoT platforms, cloud services, and advanced control systems effortlessly.
In one way, WSNs connect sensors tracking machine health with predictive maintenance software, reducing downtime. It also can link energy monitoring sensors with smart grid solutions, optimising power distribution. It is possible to sync sensors measuring chemical levels with centralised dashboards for better process control. This interoperability streamlines data sharing, simplifies upgrades, and supports real-time insights across the entire system.
Traditional wired sensor networks usually cause headaches due to their lack of compatibility with newer technologies and rigid setups. Industries struggled to connect sensors to advanced systems or add new devices without major rewiring, slowing progress and increasing costs. Wireless sensor networks eliminate these issues by offering smooth interoperability, allowing industries to link sensors with IoT platforms, cloud services, and advanced control systems effortlessly.
In one way, WSNs connect sensors tracking machine health with predictive maintenance software, reducing downtime. It also can link energy monitoring sensors with smart grid solutions, optimising power distribution. It is possible to sync sensors measuring chemical levels with centralised dashboards for better process control. This interoperability streamlines data sharing, simplifies upgrades, and supports real-time insights across the entire system.
Real-Time Monitoring and Pinpointing Areas of Errors
When it comes to industrial automation, no delay should be made in spotting and fixing problems, and wireless sensor networks excel in making this happen.
Traditional wired sensor networks struggled with real-time monitoring because they relied on extensive cabling, which limited their range and made system expansions complicated.
However, WSNs provide continuous monitoring of equipment and processes to ensure smooth operations and early detection of issues. These networks transmit data wirelessly, eliminating the need for physical connections and allowing sensors to cover every corner of an industrial setup. Industrialists can use WSNs to track machine temperatures and vibrations, identifying signs of wear before they cause downtime.
On the other hand, power plants rely on wireless sensors to monitor voltage levels and pinpoint fluctuations that could lead to outages. Plus, it is possible to monitor flow rates and detect blockages in real-time, preventing costly disruptions. Wireless sensor networks send alerts when they detect anomalies, enabling rapid response and reducing risks.
This level of precision allows industries to fix issues before they escalate, ensuring operations run efficiently.
Traditional wired sensor networks struggled with real-time monitoring because they relied on extensive cabling, which limited their range and made system expansions complicated.
However, WSNs provide continuous monitoring of equipment and processes to ensure smooth operations and early detection of issues. These networks transmit data wirelessly, eliminating the need for physical connections and allowing sensors to cover every corner of an industrial setup. Industrialists can use WSNs to track machine temperatures and vibrations, identifying signs of wear before they cause downtime.
On the other hand, power plants rely on wireless sensors to monitor voltage levels and pinpoint fluctuations that could lead to outages. Plus, it is possible to monitor flow rates and detect blockages in real-time, preventing costly disruptions. Wireless sensor networks send alerts when they detect anomalies, enabling rapid response and reducing risks.
This level of precision allows industries to fix issues before they escalate, ensuring operations run efficiently.
Utilising Advanced Wireless Sensor Networks for Optimised Industrial Efficiency
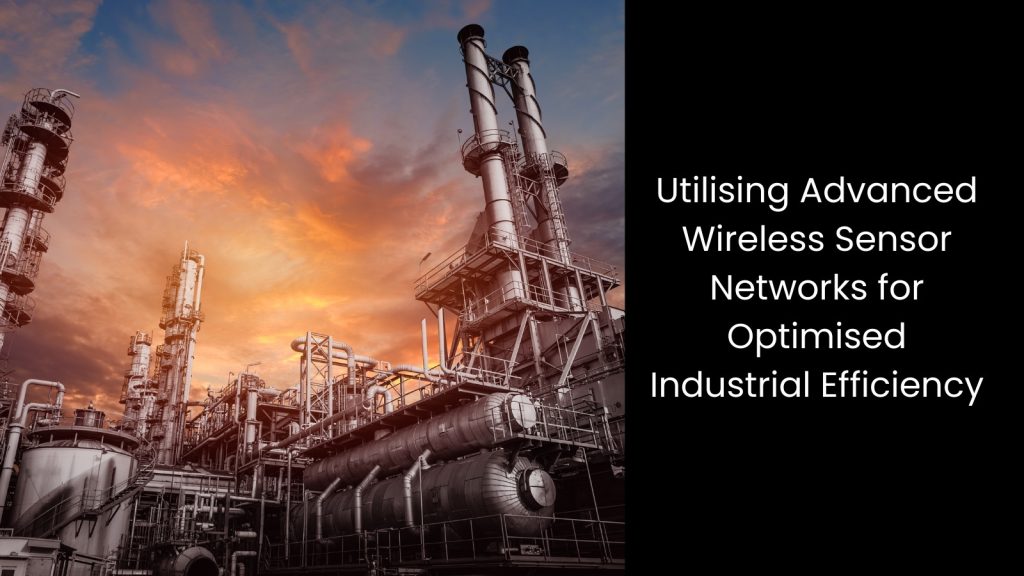
Efficiency is not just a goal but a top necessity in today’s industrial automation landscape. Wireless sensor networks bridge the gap between innovation and practicality, offering unmatched monitoring, decision-making, and process optimisation solutions. Whether tracking performance or preventing errors, these networks empower industries to operate with precision. However, you need to collaborate with an industry pioneer to receive what you expect from this.