Modern commercial construction is undergoing a rapid transformation, with technology leading the way. If you are from this particular industry, you may be witnessing this every single day! Traditional building processes relied heavily on manual labour and outdated planning methods, but today’s industry operates on automation, real-time data, and AI-powered decision-making. From technological devices conducting site inspections to advanced equipment optimising performance, construction projects now achieve higher precision and faster completion times. This is how the rise of advanced technologies has redefined the way construction companies approach design, planning, and execution.
This article explores the role of technology in the modern commercial construction landscape.
This article explores the role of technology in the modern commercial construction landscape.
We will understand
- The Growing Influence of Digital Transformation in the Commercial Construction Industry
- Key Technologies Revolutionising Commercial Construction
- Building Information Modelling (BIM)
- Artificial Intelligence (AI) and Machine Learning
- Internet of Things (IoT) and Smart Sensors
- Drones and Robotics in Construction
3. Staying Ahead with Emerging Technologies in Commercial Constructions
The Growing Influence of Digital Transformation in the Commercial Construction Industry
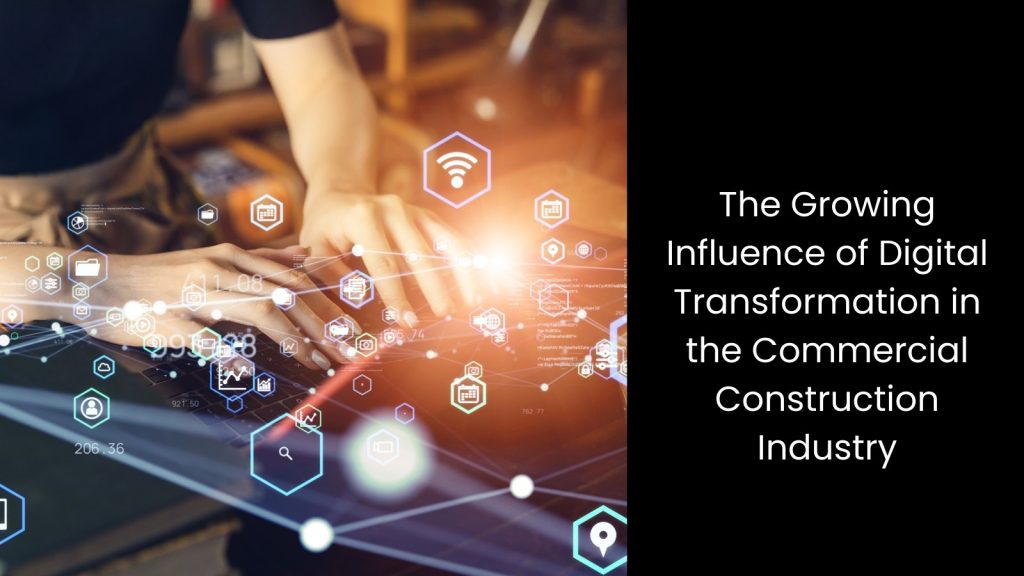
- When we go back in time, commercial construction looked nothing like it does today. People relied on manual labour, simple tools, and traditional blueprints to bring buildings to life.
- As the industry grew, so did the need for stronger materials, faster construction, and better planning. The introduction of steel, concrete, and mechanised equipment made projects bigger, taller, and more complex.
- Fast forward to today, and digital transformation has taken over the commercial construction industry. It simply makes everything smarter, faster, and more efficient. There are many technologies to improve project planning, help predict risks before they become problems and track equipment and worker safety in real time, reducing delays and accidents.
- Some advanced tools provide high-resolution site inspections, replacing slow and expensive manual checks. As you can see, embracing such technology not only speeds up construction but also cuts costs and reduces material waste, making projects more sustainable.
- These systems improve safety by monitoring hazardous areas and alerting workers instantly. It is clearly visible that the future of commercial construction depends on how well companies adapt to these advancements.
- Those who invest in modern technology will complete projects with better precision, fewer delays, and improved safety. It is a sealed promise that this will keep them ahead in an industry that never stops evolving.
Key Technologies Revolutionising Commercial Construction
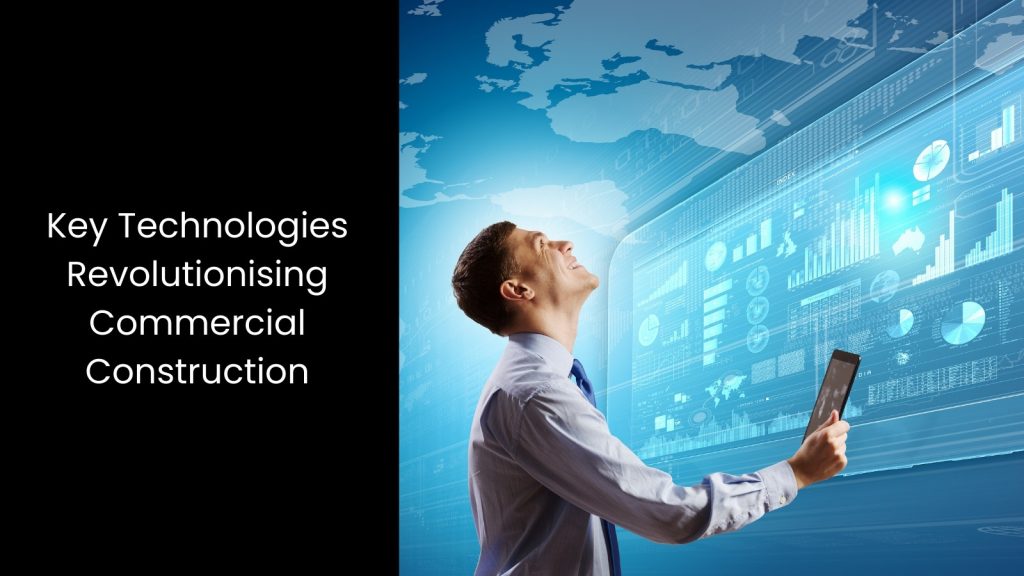
Building Information Modelling (BIM)
BIM is a mechanism of transformation in commercial construction, turning outdated project planning into a seamless digital process. Traditional blueprints usually cause miscommunication, but BIM eliminates that by creating an intelligent 3D model that keeps architects, engineers, and contractors on the same page.
Its real-time data integration lets teams track changes instantly and reduces errors before they turn into costly problems. This way, collaboration becomes smoother because everyone works on a shared model instead of juggling multiple versions of outdated plans. In another way, commercial construction projects benefit from precise cost estimation since BIM calculates material quantities accurately, preventing unnecessary spending.
As another aspect, risk mitigation improves as BIM identifies design flaws early and allows teams to fix weak spots before construction starts. Clashes between electrical, plumbing, and structural components get spotted in the virtual model, avoiding expensive fixes later. Its 3D visualisation capacity also helps clients understand the final structure before a single brick gets laid, speeding up approvals and reducing last-minute changes.
As commercial construction keeps pushing for smarter, faster, and more cost-effective solutions, BIM stands as the key to unlocking efficiency.
Its real-time data integration lets teams track changes instantly and reduces errors before they turn into costly problems. This way, collaboration becomes smoother because everyone works on a shared model instead of juggling multiple versions of outdated plans. In another way, commercial construction projects benefit from precise cost estimation since BIM calculates material quantities accurately, preventing unnecessary spending.
As another aspect, risk mitigation improves as BIM identifies design flaws early and allows teams to fix weak spots before construction starts. Clashes between electrical, plumbing, and structural components get spotted in the virtual model, avoiding expensive fixes later. Its 3D visualisation capacity also helps clients understand the final structure before a single brick gets laid, speeding up approvals and reducing last-minute changes.
As commercial construction keeps pushing for smarter, faster, and more cost-effective solutions, BIM stands as the key to unlocking efficiency.
Artificial Intelligence (AI) and Machine Learning
AI and ML are two capabilities that this industry cannot afford to ignore as they turn commercial construction into a smarter, faster, and more efficient process.
Let us explore how this works.
AI-powered project management eliminates guesswork by analysing massive amounts of data to predict delays, budget overruns, and safety risks before they happen. Predictive analytics scans past projects and real-time site data to highlight potential problems, allowing teams to fix them before they escalate. Automating design optimisation removes the trial-and-error approach, generating the best structural layouts while cutting material waste and reducing costs.
On the other hand, resource allocation becomes smoother since AI calculates exactly how much labour, equipment, and materials a project needs. This prevents shortages and overspending. Unlike human decision-making, which can be slow and error-prone, AI makes instant calculations and provides precise recommendations, reducing costly mistakes.
Have you noticed these smart algorithms analyse thousands of possibilities in seconds? That is what helps engineers and contractors choose the most efficient construction methods. Another advantage is that safety improves as AI detects hazards and alerts workers before accidents happen. AI-powered cameras and sensors track site activity, ensuring teams follow safety protocols without needing constant supervision.
There is no doubt that the construction companies that adopt these technologies will complete projects with fewer errors, smarter resource use, and better decision-making at the same time!
Let us explore how this works.
AI-powered project management eliminates guesswork by analysing massive amounts of data to predict delays, budget overruns, and safety risks before they happen. Predictive analytics scans past projects and real-time site data to highlight potential problems, allowing teams to fix them before they escalate. Automating design optimisation removes the trial-and-error approach, generating the best structural layouts while cutting material waste and reducing costs.
On the other hand, resource allocation becomes smoother since AI calculates exactly how much labour, equipment, and materials a project needs. This prevents shortages and overspending. Unlike human decision-making, which can be slow and error-prone, AI makes instant calculations and provides precise recommendations, reducing costly mistakes.
Have you noticed these smart algorithms analyse thousands of possibilities in seconds? That is what helps engineers and contractors choose the most efficient construction methods. Another advantage is that safety improves as AI detects hazards and alerts workers before accidents happen. AI-powered cameras and sensors track site activity, ensuring teams follow safety protocols without needing constant supervision.
There is no doubt that the construction companies that adopt these technologies will complete projects with fewer errors, smarter resource use, and better decision-making at the same time!
Internet of Things (IoT) and Smart Sensors
If monitoring is your challenge in construction, IoT and smart sensors turn the entire site into a connected ecosystem that tracks everything in real time. Do you wonder how?
Commercial construction projects deal with tight schedules, heavy machinery, and unpredictable risks. Therefore constant site monitoring is essential. IoT-enabled devices provide live updates on equipment performance, material usage, and worker movements, ensuring nothing goes unnoticed.
Real-time tracking helps managers spot inefficiencies, reduce downtime, and improve decision-making. As a giant part of this, preventive maintenance gets a major upgrade with IoT-connected equipment that detects early signs of wear and tear before breakdowns happen. Instead of waiting for a machine to fail, smart sensors send automatic alerts, allowing teams to schedule repairs at the right time and avoid costly delays.
Worker safety also improves with smart wearables that monitor heart rate, fatigue levels, and exposure to risky conditions. If a worker shows signs of heat stress or enters a dangerous zone, the system sends an immediate warning. This capability prevents accidents before they occur.
As commercial construction pushes for more efficiency and safety, such advancements in the industry keep projects on schedule without unnecessary setbacks.
Commercial construction projects deal with tight schedules, heavy machinery, and unpredictable risks. Therefore constant site monitoring is essential. IoT-enabled devices provide live updates on equipment performance, material usage, and worker movements, ensuring nothing goes unnoticed.
Real-time tracking helps managers spot inefficiencies, reduce downtime, and improve decision-making. As a giant part of this, preventive maintenance gets a major upgrade with IoT-connected equipment that detects early signs of wear and tear before breakdowns happen. Instead of waiting for a machine to fail, smart sensors send automatic alerts, allowing teams to schedule repairs at the right time and avoid costly delays.
Worker safety also improves with smart wearables that monitor heart rate, fatigue levels, and exposure to risky conditions. If a worker shows signs of heat stress or enters a dangerous zone, the system sends an immediate warning. This capability prevents accidents before they occur.
As commercial construction pushes for more efficiency and safety, such advancements in the industry keep projects on schedule without unnecessary setbacks.
Drones and Robotics in Construction
These are two emerging trends in commercial construction which make projects faster, safer, and more precise.
First, let’s take drones. The latter takes aerial site inspections to another level, capturing high-resolution images and mapping vast areas in minutes instead of days. Project managers no longer need to rely on slow manual surveys or risk climbing unsafe structures to check progress. With real-time drone footage, their teams can track developments, detect structural issues, and keep everything on schedule without second-guessing.
Robotics, on the other hand, takes care of repetitive tasks that slow down human workers. Bricklaying, concrete pouring, and even demolition become faster with automated machines that work around the clock without fatigue. These robotic systems ensure consistency, cutting down on human errors that lead to costly rework.
There should be no compromise when it comes to large-scale commercial projects, as they demand extreme accuracy. This is where drones combined with robotics help achieve that. Advanced sensors and AI-powered machines analyse measurements with pinpoint precision, ensuring structures align perfectly with blueprints. Excavation robots dig with exact depth calculations, while robotic arms handle materials with the right force, reducing waste and improving efficiency.
As commercial construction embraces smarter technology, drones and robotics will continue transforming the industry even after another 20 years. What do you think?
First, let’s take drones. The latter takes aerial site inspections to another level, capturing high-resolution images and mapping vast areas in minutes instead of days. Project managers no longer need to rely on slow manual surveys or risk climbing unsafe structures to check progress. With real-time drone footage, their teams can track developments, detect structural issues, and keep everything on schedule without second-guessing.
Robotics, on the other hand, takes care of repetitive tasks that slow down human workers. Bricklaying, concrete pouring, and even demolition become faster with automated machines that work around the clock without fatigue. These robotic systems ensure consistency, cutting down on human errors that lead to costly rework.
There should be no compromise when it comes to large-scale commercial projects, as they demand extreme accuracy. This is where drones combined with robotics help achieve that. Advanced sensors and AI-powered machines analyse measurements with pinpoint precision, ensuring structures align perfectly with blueprints. Excavation robots dig with exact depth calculations, while robotic arms handle materials with the right force, reducing waste and improving efficiency.
As commercial construction embraces smarter technology, drones and robotics will continue transforming the industry even after another 20 years. What do you think?
Staying Ahead with Emerging Technologies in Commercial Constructions
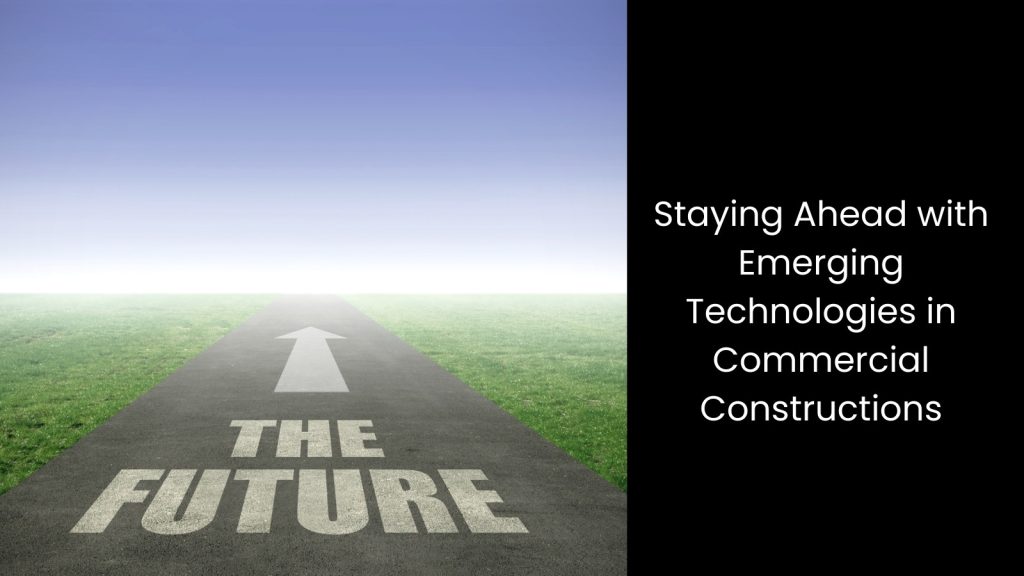
The future of commercial construction belongs to those who embrace emerging technologies. Smart solutions that integrate Industry 4.0 capabilities like AI, sensors, IoT, etc. easily offer predictive analytics, automated resource allocation, and seamless collaboration. With real-time insights and AI-driven decision-making, your projects will run smoother, safer, and more efficiently. You can stay competitive by adopting a platform that pushes construction excellence to the next level. Why still wait?